Getting the basics right: Installing Architectural shade fabric.
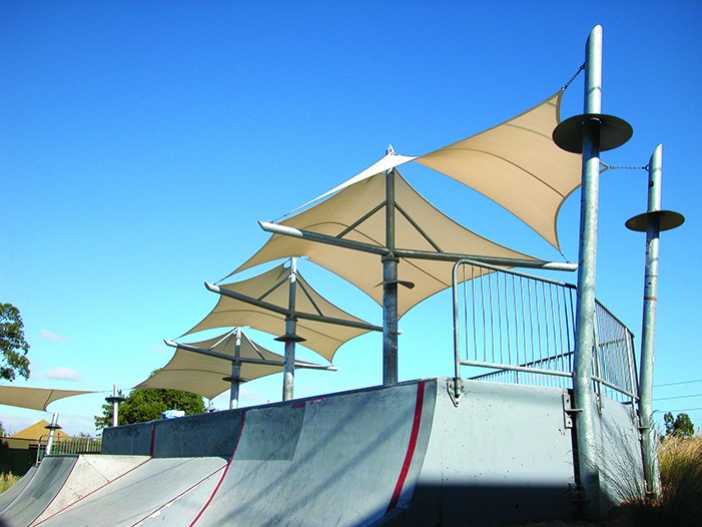
Installing Architectural shade fabric starts with getting the basics right. To get the facts, we interviewed Garth Graham. With over 40 years’ experience in the fabrication of Architectural shade – he shares his insights on ensuring the quality of large scale fabric structures.
Our interview with Garth Graham.
When it comes to the selection of webbing and cables for your structures, what do you choose?
This should be based on the required engineering design strength for the perimeter edge, and the expected working life of the edge material. Marine grade polyester webbing, with its increased UV resistance, in black or white is a good option. Ensure that the weave is of a very tight and firm construction, with minimum elongation.
I also ensure that catenary edge cables are not too small, as they cut through the fabric. I find that an 8mm outer diameter of PVC coated wire running through a reinforced edge pocket is the best system with cables.
What Stitching techniques do you use when joining panels?
The best engineered method is to use the PTFE sewing threads of a 210 size, or at the very minimum a coated polyester sail making thread.
There should be at least two rows of sewing thread used in a zigzag stitch in all seams. The use of zigzag stitching allows for elongation and recovery of the sewn thread when the panel cloth stretches under working loads.
Normal lock stitching is often used, but breakage of the straight threads when the cloth elongates under working loads is very common.
How do you choose what type of thread to use?
The best threads are the UV resistant multi-filament types in the largest denier available.
Size 210 is the best option in our experience. PTFE or PVDF thread is the best solution closely followed by coated polyester sail thread.
How do you determine the optimal catenary curve allowance?
Catenary depends on the engineer’s design in relation to the span of the panel, the location, the building codes and the required pre-stress. Usually a minimum of 6% to a maximum of 12% is workable for a shade cloth panel.
When do you use double curvature?
Double curvature is a basic ingredient in good fabric architecture, it is also known as anti-clastic curvature. It is used in most fabric structures to provide stability to the membrane e.g. Hypar or barrel vault slopes.
However, it is not an essential requirement for smaller tensile structures because the details on small structures are fairly straightforward. On larger structures there is a lot of careful engineering and detailing required to ensure that the corner fixtures can be pulled into position while under high loads.
Do you use biaxial stretch data prior or during installation?
Yes, we do. The best system for evaluating a cloth’s performance in terms of strength and stretch is a biaxial test. The cloth is subject to loadings in the warp and weft direction simultaneously.
Shade cloth manufacturers should supply this information to enable engineers and fabricators to accurately design and fabricate. At the point of installation, the installer should use a dynamometer to record the tension on the edge cables, or webbing as they are installed.
This is so they are aware that the actual pre-stress loads for the cloth panel has been set accurately according to the fabrics biaxial characteristics. Normal pre-stress tension for a shade cloth could be up to 2kN per meter.
What is the minimum angle to install shade fabric?
The angle of the cloth panel is determined by the consultation between the consumer’s requirement and the engineer’s design requirement for the location.
How do you select D-shackles for your installations?
An engineer will need to determine the required hardware as it must meet the load requirements from the cloth panel into the support columns and allow for re-tensioning in time.
Corners of the cloth panel must be reinforced so they can transfer working loads into the corner termination hardware. Normally an extra layer of the shade cloth or PVC cloth is sewn onto the corner area of the panel. PVC/Polyester fabric is generally stiff and can be used as a reinforcement for corners.
How are the post requirements for installations determined?
An engineer will determine the post requirements.
The columns/posts can be either circular, square, rectangle, a hollow section of steel pipe/tube, or even a truss section to suit the architectural design intent.
The size of the steel components will relate to the loads that the cloth panel can apply during an extreme event, such as high winds or high hail loads.
How are footing requirements determined?
An engineer will determine the footings required, as they will vary with each installation depending on both the size of the shade sail and posts, but also the location.
In locations with high wind zones stronger footings will be required. The design can be for piers, spread, or chemical anchoring into an existing concrete pad.
The soil conditions at the location are also an important factor in the choice of footings. Ideally soil test data is requested to identify any challenges and extra costs that may be incurred on site.
How do you determine the different pre-stress levels for different grades of shade cloth i.e. light, medium and heavy?
We engage an engineer to determine pre-stress areas, as they depend on the area covered, the shape of the panel as well as the grade of shade cloth.
The fabrics tensile and weight properties, and the spans and the shape of the installation will determine the pre-stresses. Location and building codes will also influence what cloths are suitable for specific locations.
How do different locations affect how a shade sail is designed and installed i.e. high wind zones?
This is something a qualified engineer will need to review as it relates to building codes. Use a registered engineer who has experience with tension structures and is qualified to work in your area. It is best to get site specific designs and a certificate of design for all structures.
What care and maintenance recommendations do you provide your customers?
Shade cloth should be set at the engineers required pre-stress to control any movement of the cloth under extreme weather loads and minimise sagging over time.
In regards to keeping the cloth clean, it can be hosed with water and a mild detergent as required, to keep the cloth panel clean and free of dirt build up. Shade sails and waterproof structures are light weight constructions using fabrics with specified life spans.
Their low cost, flexibility and aesthetics make them popular. This being the case, they do need to be inspected and maintained from time to time to keep them functional and looking their best.
What codes and standards need to be considered?
The key codes and standards I reference are:
- AS1170.2:2011 – Specifies structural design actions, general principles and wind loading codes
- AS4100:1998 – Steel structures code Building Code of Australia
How are fabric shade structures more sustainable than traditional solid roofed structures?
Shade structures using shade cloth are lighter and require fewer raw materials in their manufacturing process. Therefore, they have relatively low energy consumption compared to traditional solid roofed structures.
We recommend shade fabrics that are Oeko-Tex and Greenguard certified to clients looking for sustainable solutions.