Case Study: Ipswich Rugby Leagues Club
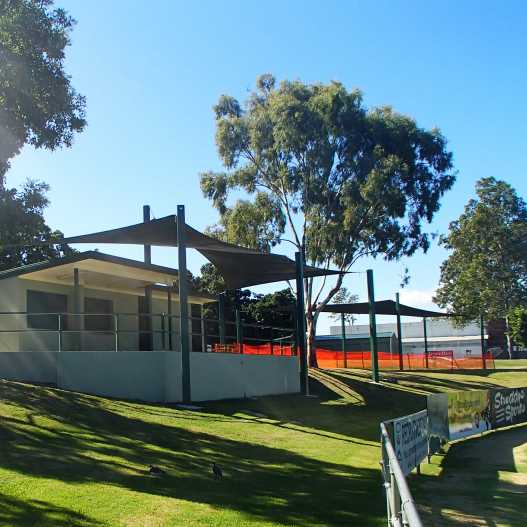
The following report, based on a new shade sail installation at Ipswich Rugby League Club (Qld, Australia) was prepared by Peter Kamols, leading expert in membrane structure design.
Commercial Heavy 430 was selected for this project as the fabric exhibits less stretch over time compared to any other shade cloth in the market and the westerly storm front exposure, which ensures the sail will stay tighter for longer before the sail may need to be re-tensioned. 'Brunswick Green' was chosen to compliment the existing colour theme of the buildings.
UV radiation is the main cause of degradation of shade cloth, sewing thread and webbing and it is strongly recommended that only the best quality UV resistant products be used, as is the case with this structure.
The Design
The installation has a total plan area of approximately 85m2 of covered area in the form of an approximately rectangular sail with 6 connection points. The sail is designed as a twin-hypar shape with five low points and one high point in the middle of the long northern side.
Square section steel cantilever columns set into concrete bored piers were chosen for support so as to minimise the interruption of sight lines. Backstay cables were not an option as they would have represented an unacceptable trip hazard in a public space. On the columns, the attachment system includes a threaded eyebolt and chain.
It was considered that the new Commercial Heavy fabric was the best choice for the sail which overlaps the existing building and is required to stay tight and minimise deflection under wind load so as to avoid a clash with the existing Kiosk roof.
The high point on the northern side allows some sun to penetrate onto the deck during Winter but not during Summer. Low edges on the shorter East and West sides provide good sun control during all seasons.
Shade cloth compensations and pre-stress
Bi-axial testing of Commercial Heavy 430 shade cloth has shown that a fabric compensation of approximately 1.2% in both warp and weft at a prestress load of 1.2kN/m is appropriate. This effectively means that the shade cloth was patterned to be 1.2% shorter in both warp and weft directions to allow for an elongation of 1.2% under prestress.
Commercial Heavy 430 biaxial test results
All other heavy duty shade cloths on the market would have required very different compensation percentages between the warp and weft directions.
The fabric engineer chose a prestress of 1.2kN/m with a catenary depth percentage of 10% for this sail. This means a catenary depth of 100mm for every metre of length along a side.
As always, the choice of edge cut percentage is a balancing act between reducing load and reducing the shade area. The greater the edge cut, the lower the loads generated but also results in a reduction of shaded area.
Perimeter and corner details
The engineer has detailed a webbing edge consisting of two layers of 50mm UV stabilised polyester marine grade webbing. One layer above the shade mesh and one layer below with the shade cloth sandwiched between.
It was found from testing that the two layers combined to have a rate of stretch which was highly compatible with the stiffness of the shade cloth. The two layers of polyester marine grade webbing are then taken around the double stainless steel Dee rings in the corners and sewn back on themselves. This is then reinforced with an additional layer of webbing which is taken through the stainless steel Dee rings and again sewn back over the previous layers. This is then terminated with a pair of 50mm x 50mm galvanised steel plate washers and a structural galvanised clamping bolt, which is passed through the webbing and the two plates are firmly clamped together to provide an additional high-friction mechanical fixing.
The webbing is sewn using four rows of Fluorocarbon thread stitching. The Fluorocarbon thread used for the stitching is very strong, is not affected by UV and outperforms any other available thread.
Shade sail corner detail
Tensioning system
All corners have a combination of an adjustable galvanised eyebolt which is taken through the powder coated SHS column and an adjustable length of galvanised chain with galvanised tested shackles both ends.
The sail is tensioned by winding the eyebolts and adjusting the chain links so that the eyebolts are pulled up to the face of the SHS when the sail is at full pre-tension. It is best to always attempt to pull a threaded eyebolt up against the surface through which it is being drawn so that there are no bending loads imposed on the threads of the adjusting eyebolts.
Should the sail require re-tensioning at a future date the eyebolts would be wound out enough for a chain link to be removed from the chain and the eyebolts and the now shorted chain again wound back to the face of the SHS columns.
Tensioning at columns
Installation
Commercial Heavy 430 shade cloth was chosen because it was the best balanced heavy duty shade cloth on the Australian market. It makes the installation less reliant upon a carefully managed sequence of attachment tensioning required by other shade cloths which have widely varying rates of elongation between warp and weft. The sail will also require less re-tensioning during the life of the sail.
The balanced compensations of the shade cloth sail made the tensioning of the sail very simple as the attachments were all tensioned gradually and concurrently, providing an even prestress throughout the sails.
Fabricators comments
- “The fabric appears to be holding its cut length throughout the process and all seams came together and matched perfectly."
- “The fabric does not curl and is easy to handle at the machine. Using an Adler twin needle compound feed machine there were no problems. The number 26 needles caused no filament breakage so the strength should be excellent.”
- The fabric was moved a lot on our table. All edges have been cut with a hot knife. It has been folded a number of times and ended up being folded up and stored on site for over a month until other works were ready but it still tensioned out well with no wrinkles or visible fold marks.
Commercial Heavy 430 shade cloth and the sail shape, webbing, detailing and tensioning system has worked very well.
Efficient and quick installation has resulted in an even level of prestress in all directions. The long term performance is expected to be favourable and superior to other monofilament shade cloths on the market since the Commercial Heavy 430 shade cloth;
- Better retains its physical properties, design shape, safety factors and structural reliability over time which contributes to lower stretch over the life of the shade cloth structure.
- Requires less re-tensioning and thus is less likely to run out of adjustment at attachment points during its lifetime and,
- Better retains its UVR Block Percentage and Shade Factor throughout the life of the shade cloth because less elongation (stretch) means the voids between threads undergo less enlargement compared to all other shade cloths that have greater elongation.
The installation will be revisited in one year or after any severe wind event should one occur before twelve months.
Peter Kamols Bach. Architecture (1st Hons)
Kamols Designs Pty Ltd